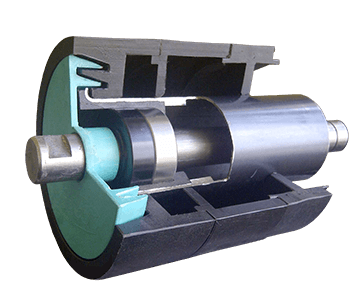
Cobra HDPE High Density Polyethylene Conveyor Rollers
This uniquely designed roller incorporates a patented sealing arrangement, bearing, seal housing and roller shell. HDPE rollers are designed for harsh operating conditions, extreme temperatures and even corrosive, chemical or coastal, conditions. HDPE idlers are lubricated for life and are a better alternative to traditional steel rollers for these applications. They are available in standard, anti-seize and anti-run-back variations.
Differences between Steel Idlers & HDPE Idlers
Coefficient of Friction
Rubber to Rubber 1.15
Rubber to Steel 0.7
Rubber to HDPE 0.4
Steel Idler VS. Cobra HDPE Idler
- Higher coefficient of friction vs Cobras’ Lower coefficient of friction
- Less concentric vs Cobras’ more concentric
- Weight (weighs more) vs Cobras’ weight (weighs less)
- Not belt friendly vs Cobras’ belt friendly
- Corrosive vs Cobras’ not corrosive
-
Higher running friction vs Cobras lower running friction
-
Coefficient of friction With the steel idler having a higher coefficient of friction there is more heat being generated if there is idler seizure. If there is idler seizure the steel idler is also more likely to damage the belt. The steel idler will gradually eat away at the belt whereas with the HDPE idler, the belt would rather eat away at the idler, prolonging belt life by reducing the chance of the idler damaging the belt.
-
Concentricity Due to bearing caps being welded in and no machining being done to the diameter of idler after assembly, bearing alignment and concentricity of a steel idler cannot be achieved. Due to the bearings being inside the inner tube of the CMI HDPE segmented idler and the Idler being skimmed after assembly, near perfect bearing alignment and concentricity can be achieved. It then goes without saying that with better bearing alignment and idler concentricity there will be less vibration, less noise, prolonged bearing life, less running friction, less wear on idler, less damage to belt.
-
Weight Due to the HDPE idler being considerably lighter than the steel idler the breakaway mass of the steel idler is considerably higher than this of the CMI HDPE segmented idler. The CMI HDPE idler was tested at an average of 58.3 grams. In a feck this means that the conveyor will use less power to start up because there is less resistance to get the belt going. This combined with the lower coefficient of friction between the HDPE and the rubber belt means that the running friction is less. The CMI HDPE idler was tested at 0.94 newton force after 30min running-in period and 2.54 newton force after 60min rest period. The running friction being less combined with the HDPE segments being injection moulded gives us less wear on the diameter of the idler in return giving you longer idler life.
-
Belt Friendly We have touched on this in the previous points. The belt would rather eat away at the idler than the idler eat away at the belt This means that the belt would not be damaged if the idler should stop turning for whatever the reason .This is a major advantage as for the cost saving of production loss and belt replacement
-
Corrosion A big advantage of the HDPE idler to the steel equivalent is also that it is corrosion free. This is extremely helpful on belts where there is excess water present. The unique sealing that the CMI HDPE segmented idler has disperses water as the idler turns. This is achieved with the deep tapered grooves on the idlers primary seal. In addition to this seal a secondary seal (3-part labyrinth seal) is also fitted, preventing water and dust from getting into the rubber sealed bearing (2RS).
- Running Friction We have also touched on this subject in point 1. Due to the higher coefficient of friction between rubber and steel and the higher breakaway mass there is more friction between the belt and the idler. More friction equals more heat and more wear between the belt and a steel idler than between the belt and an HDPE idler.
Mining Sites where Shaw Almex Segmented HDPE Idlers have been installed successfully:
- Foskor Phalaborwa- Drying & Dispatch
- Palaborwa Mining Company (PMC)- Magnetite Separation Plant
- Middelburg Ferrochrome (Samancor)- Pelletizing & Sintering Plant (PSP)
- Tubatse Chrome Steelpoort (Samancor)- Pelletizing & Sintering Plant (PSP)
- Glencore Xstrata Lydenburg – Pelletizing & Sintering Plant (PSP)
- Langer Heinrich Uranium – Namibia
- Kroondal 2 – Minopex Rustenburg
- Mortimer Smelter – Union Mine Anglo American